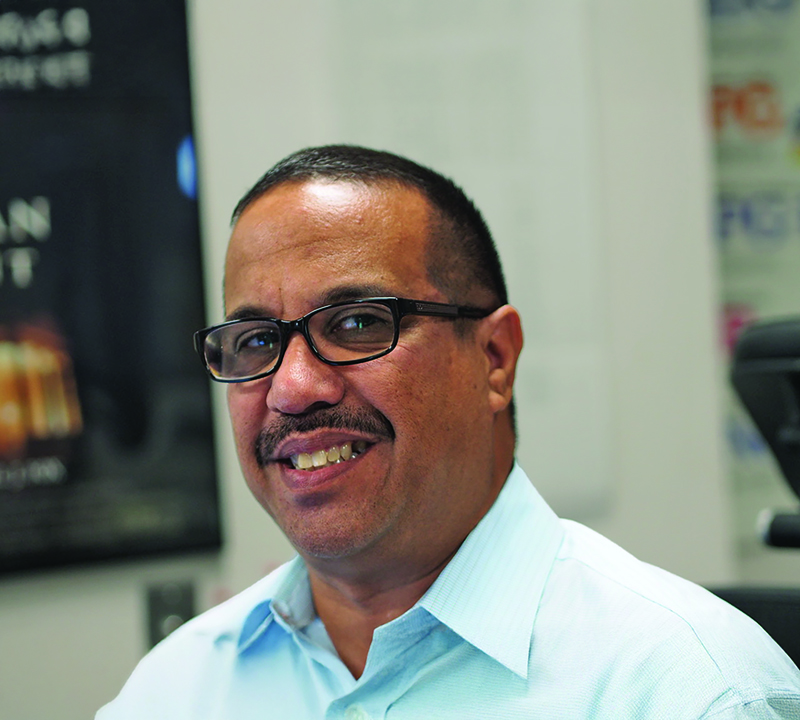
by Mark Ulano CAS AMPS
Joe Aredas, Jr., Assistant Business Representative for IATSE Local 695, is an essential partner of the team representing the union members the Local since 2012. He works closely with Business Representative Scott Bernard and Co-assistant Business Representative Heidi Nakamura. Joe, himself, a long-standing member of our union, also has also served the Local as an elected member of the union’s Executive Board since 2006 and he continues to make important contributions on the Industry Safety Committee, working to keep our members safe at work.
MU: Joe, I’m curious about your basic responsibility. as a rep? How long have you been serving members?
JOE: I’ve been a rep for, let’s see, going back to 2012. So I’ve been a representative since then, before with Local 700, of course. And then I’ve been a Board member since 2006. Right off the bat, let me say that Scott, Heidi, and I all work in unison representing our members at the Local, at the IATSE, and at the political level. It is a solid team covering all the bases.
MU: Didn’t you serve as president in another local in a prior period of your life?
JOE: That is correct, Local 683.
MU: There’s depth to the kinds of information and knowledge you bring to the table. That’s important, I think, for people that they have that going on behind the scenes. What would you say is the most common service you provide?
JOE: I would say interpreting the contract for members because a lot of people have questions.
MU: That’s a key point. I remember in my time working with you that of anyone on the staff, you were most likely to have direct memory of language in the variety of contracts that we must service and enforce.
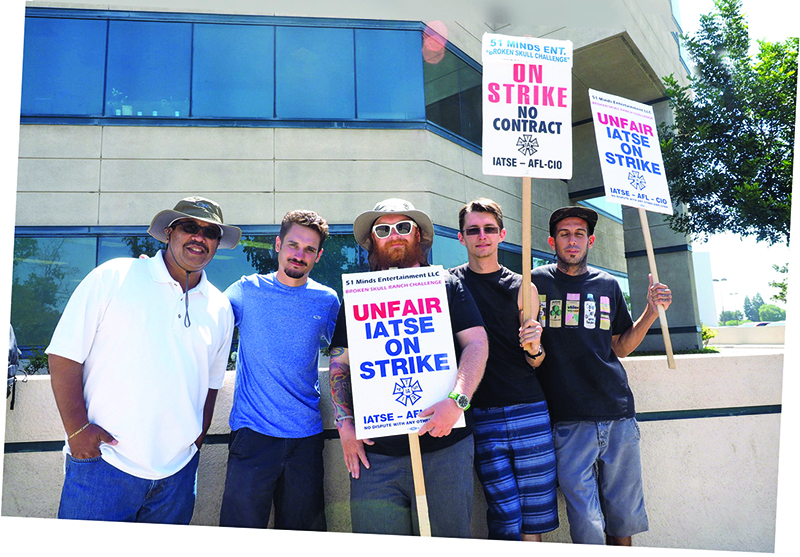
Can you describe a typical day or week of your job?
JOE: I’m a person who plans for the most part. I like to plan out my week and then leave time in the week for anything that I need to respond to. I try to plan for at least a couple of days for set visits each week. I try to schedule those in advance. I also must constantly check my emails for any questions that may come in.
A great thing that’s been going on for a while is we have a general rep email that questions go to. This way, Heidi, Scott, or I can look at that. One of us will usually answer and cover copy each other so all of us are aware, again, keeping our team fully informed.
MU: Visits? You mean production sets and fixed facilities? Is that the answer?
JOE: Yes, that is correct. There may be something problematic, but a lot of the time I am just checking in on our members, their well-being, connecting, and generally just checking in with production and fostering relationships with producers if I can, and to make sure that when I take a position, if there is an issue, that it’s easier to address with someone that you are trying to partner with.
MU: Do you have any special skills or history that really help you with your support for members?
JOE: I think my family history would be important. Being around my father, I learned a lot from him about how to get the job done.
MU: And your brother Steve, too. He’s an important part of the IA’s West Coast Office team in the field. Your dad, Joe Aredas, Sr., has special history in more ways than as a member. Joe, Sr. was a longtime rep here at Local 695, then became the head of the IATSE West Coast Office for many years. He’s been in leadership for many years, former head of the West Coast Office, now retired and for me personally was a very important mentor and guiding spirit at the very beginning of my and my wife’s coming into the union.
JOE: Was that in the ’80s?
MU: Yes, it was 1983 to be exact.
How would you describe your relationship with the members?
JOE: I would say I strive to connect with our members professionally. I really attempt to connect personally. It’s important to remember who they are and what is going on with them if I have that information, you know, like their family may just have had a kid. Or they are not working as much and how can I help them? That kind of stuff. I try to genuinely connect with our members the best I can.
MU: Do you continue with ongoing training for different aspects of the work?
JOE: I have taken all the IA training that I could for organizing. I strive for safety training myself. I just finished the OSHA 30. [Editor’s note: OSHA’s 30-day safety training course.]
I try to think of safety all the time. I am on the Contract Services Safety Committee and working with developing their bulletins. I was lucky enough to be involved with the ergonomic long, takes bulletin. [Editor’s note: These guidelines protect Boom Operators and other crew members subject to unsafe extended takes. The bulletins are agreements between labor and management that define safety protocols for the industry and are supposed to have the teeth of enforcement.]
MU: Yes. We have some history together serving on the Safety Committee for several years. I know you were the front end of the Local for that journey. And it took a while, but it bore fruit by having that become a proper bulletin as opposed to the lesser guidelines. That was a very important moment, a real achievement.
JOE: I always hope that the members learn about that kind of stuff and read about that stuff. It’s all available online now. It’s all changed since I started. And sometimes we’re bringing up things that we think need to be in a safety bulletin.
As the changes take place, the Safety Committee will make changes as well.
MU: Can you give me a little bit of information about the OSHA 30 training that you’ve just completed and what it brings to the membership?
JOE: Well, there’s an OSHA 10 class and an OSHA 30 class. I thought I have been on the Safety Committee; I really need to commit to this training. A lot of it was very important to listen to. Right now, they’re coming out with a new safety advisor position. This is a new law in California, so a lot of people were taking this training to try to qualify for that position. The training went through pretty much every facet of safety that we could go through and in great depth. Other topics are certainly included like sound hearing protection, fall protection, harassment training, including bullying.
MU: What does the 10 versus the 30 numbers mean for the OSHA training? [Editor’s note: OSHA stands for: Occupational Safety and Health Administration, a US Department of Labor agency.]
JOE: The 10 is for 10 hours and 30 means 30 hours,
MU: When a member calls and needs help, depending on what the need is, what’s your process? How do you deal with that as it’s coming in?
JOE: I will speak with a member, read what they say, and open a track on my computer. Sometimes it’s a black-and-white situation that I’m able to answer. And sometimes there’s a little bit of interpretation required. It depends.
MU: Can we talk a little bit about Weingarten Rules? There are situations where you must represent members. Can you describe a little bit of that for me, and what a member can expect or ask for if they feel they’re having a problem or a crisis at work?
JOE: I will represent at a moment’s notice or talk to the company about scheduling any meetings. Any type of meeting that must take place. And there’s been a change in the last, I’d say, six or nine months with meetings. Years ago, you would never, an Assistant Business Agent or a Business Agent would never meet with human resources slash employee relations. There’re times when we’re included in those meetings. It used to be I would just deal with a labor relations person. But in the last six or nine months, there’s been meetings. And I think for the better, to be able to attend those meetings. To structure different employee relations or human resources.
MU: What do you think caused that change?
JOE: I think it’s an employer who is looking at things differently now. I do think it’s better for safety. I think more things are openly discussed or any type of investigation goes deeper. They’re looked at and explored. Things are addressed now. I think the employers are addressing a lot.
MU: It sounds like it’s a good thing in motion. These are troubled times on a lot of levels and in other arenas, but what you’re describing is not a small move forward, having a deeper collaboration in terms of representing the members with the employer. I’m glad to hear it.
You just explained that you’ve been in training with OSHA and other things. How does that turn into something practical when you’re dealing with individual members?
JOE: It could be anything from, “Hey, we don’t have a bathroom anywhere near us,” or “Hey, we’re working in a junkyard today and it’s kind of scary.” We will address any safety concerns, and they do need to be investigated. After the recent passing of a Local 728 member, I think there’s a heightened sense of making sure our members are safe.
Accidents do happen, but we need to make sure that we are doing our best to prevent and respond to these safety concerns.
MU: It’s common for working members to forget that movie and TV sets are industrial work sites and they have a variety of areas which can create danger if you’re not aware and trained how to deal with concerning situations.
JOE: Film workers for the most part do feel a sense of calmness and like this is what we do.
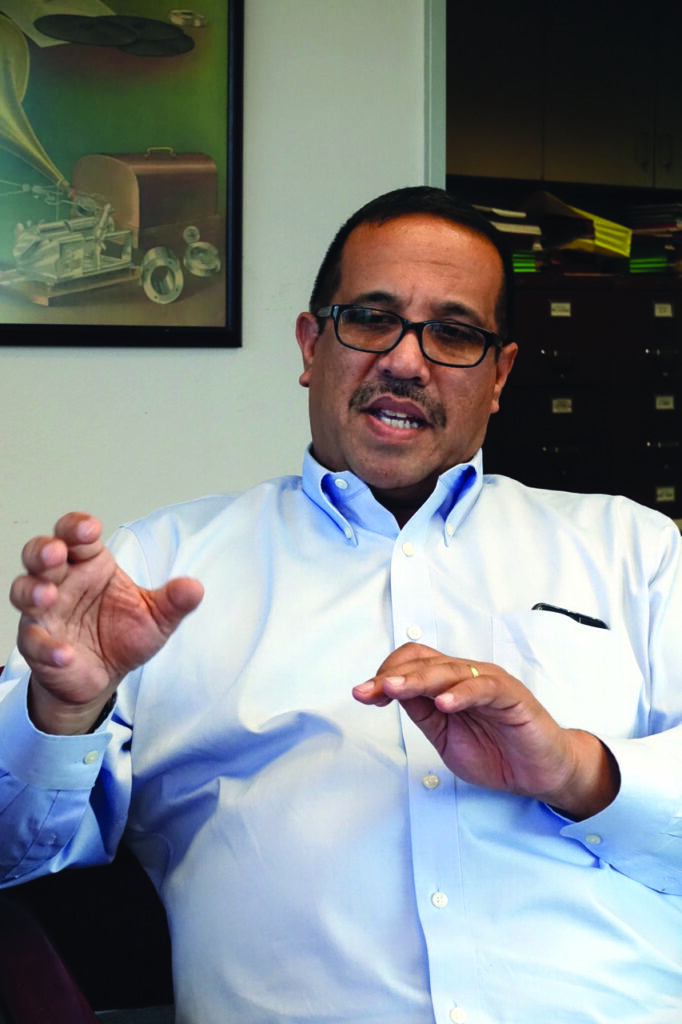
MU: In my life experience, I’ve witnessed death and severe injury on sets from accidents and other things that are traumatizing and yet very educational about what you need to do to be on guard for your own safety beyond even training. Sometimes there’s that sixth sense, that third eye, to be aware of something that may not be immediately obvious and over time become aware. I think your job probably brings a kind of connection to that awareness. For example, if you visit a set, and there’s an issue you recognize that might not have been apparent to others, it’s time to speak up. That’s a very important educational moment for members and management, I think, very important.
JOE: I’ve shown up saying, “Hey, I’m part of the Safety Committee and I just wanted to look into this to make sure.” That is something I take very seriously.
MU: What would you say is the most difficult part of your job? Not in a negative sense, but one of the bigger challenges?
JOE: I’m looking at a couple of scenarios. Let’s see. One is when someone outside of our Local is performing our work. That’s a thing I don’t like to deal with it, but it’s so problematic.
The other one is member-on-member conflict, whether it’s just member-on-member bullying or worse. I hate that more than anybody.
MU: I went through the training that the International provided over such issues and the special protocols required when we have members versus members in a conflict situation. Respect is required for A, the person making the allegation, and B, the person who’s being alleged against. It’s important to stay in the information and neutral mode when looking at that. We’ve got to protect everyone’s rights.
JOE: Or it could be a producer or anyone too, so we must really take care.
MU: What’s your vision for the future? What may be coming down the pike that’s important for us to know about?
JOE: Well, I like to see us all working together and with our sister Locals, and I think that is going on in Hollywood right now, where building relationships, I think Local 695 does enjoy a good relationship with all the locals in the IATSE.
MU: You bring an optimistic voice in these times.
JOE: I am optimistic about that.
MU: What advice can you give to anyone considering entering a career like yours as a rep?
JOE: I think that it’s a navigational job to me. You must navigate and listen and focus on the real problem that you’re listening to. You’ve got to whittle things down.
MU: You just described a successful negotiation. My training has been along the lines of the HARVARD Negotiation Project. [https://www.pon.harvard.edu/category/research_projects/harvard-negotiation-project/] This is when the opposite sides of an issue adapt to working together to solve the issue, instead of seeing each other as the enemy. Psychologically, it’s the first step toward conflict resolution. Joe, you’re on the front lines of that work.
I’m wondering if you have a sense that mentorship enters your work? Do you find yourself in some way mentoring others?
JOE: Oh, yeah, I am mentoring others, not full time, but anyone who asks me a question, I’m always willing to give my point of view and guidance.
MU: That’s beautiful.
It’s hard to have perspective when you’re under economic duress. The industry has gone through cycles of boom and bust for all the time it’s existed, and this is one of those. The business models are reshaping because they’re not functioning the way they’re intended. People tend to think everything’s running away to another region, but in fact, all the regions are seeing a severe contraction of work right now.
JOE: That is one hundred precent right, Mark. I’ve heard from people talking to me going, “Well, a bunch of it’s in New Mexico with Netflix.” But in reality, the IATSE reports that overall production was down and there were two low-budget features and one series shooting in that state. Just a few projects running over there. One show and two low budgets that are shooting for thirty days.
MU: Even Europe is very down in its production schedule.
JOE: Oh yeah, that was the other thing. Well, “England took it all.” No, that’s not true. Not true. They’re going through some of the same things we are.
MU: Do you like what you do? Are you happy in your work?
JOE: I’ve never been more satisfied at a job in my life. That’s key. I felt that I kind of fell into my groove after a while and enjoyed it to the fullest.
MU: One last question. What, if any, message or comment or expression would you like to express to members?
JOE: I think that we’re in a cycle, My father, Joe Sr., has said everything goes in cycles, and our business goes through cycles as well. It’s a strong business and it’s here to stay. There are always changes and cycles and morphing that goes on, but we will go forward…
Weingarten Rights are the legal protections for union members to have a union representative present during an investigatory interview with management where they could reasonably believe discipline or other adverse consequences may result from what they say.